Ultrasonic and Pressure Sensors
Introduction
The introduction of IoT allows a wider choice of technical solutions, but it increases the complexity of the installation options. SilentSoft Customer Service Specialists take care of the whole project management for the installation campaign, covering device availability for the installers, appointments with site managers and interfacing with customers on specific requests. With more than 20 years of experience in installing telemetry solutions on tanks, SilentSoft has built a European network of trained installers. We invite you to contact us to see how we can best help you manage your IoT project for bulk tanks.
From the very start of tank telemetry in 2000, two main sensor technologies have existed to monitor liquids in tanks: ultrasonic and pressure sensors. With 20 years’ experience in telemetry installations, SilentSoft is sharing practical use cases where the installer may select the best implementation.
How do the sensors work?
Pressure sensors are placed at the bottom of the tank, measuring absolute pressure and sometimes temperature. The pressure at the bottom of the tank is compared with another pressure sensor in the transmitting device (we call this solution differential) or with pressure information coming from weather monitoring sites. The pressure difference allows to calculate a product height taking into account the density of the product inside the tank. The product volume is calculated with the tank geometry and dimensions.
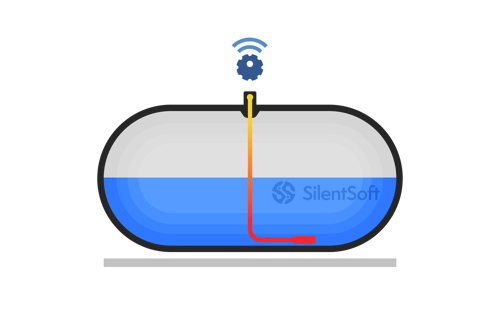
Ultrasonic sensors measure the absence of product in a closed environment (like a liquid in a tank). The product height calculation is made taking the tank height (up to the Safety Fill Level – SFL -) subtracting the absence of product. There is sometimes need for an offset if there is a difference between the bottom of the ultrasonic sensor and the Safety Fill Level.
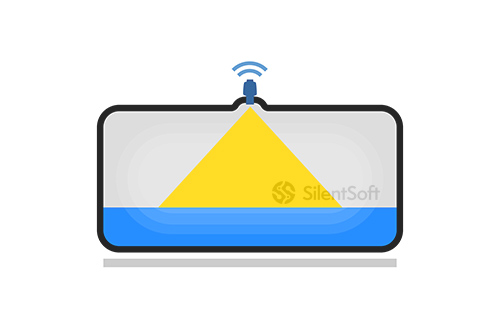
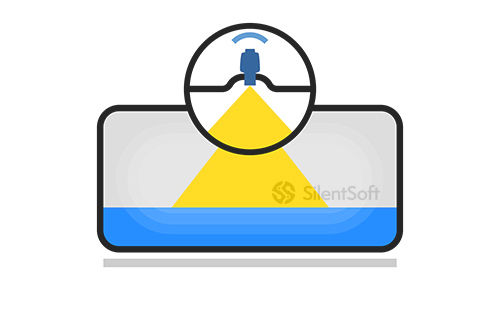
What are the technical differences?
The pressure sensors used by SilentSoft have a precision of +/- 3mbar with a measure spread of 800 to 1400 mbar. There is need for a different type of sensor if the tank is at an altitude of more than 1500m or if the tank height is over 4m.
Ultrasonic sensors have a precision of +/- 2cm and do not need any outside pressure information. There may be slight differences due to temperature variations as the monitored product may expand.
Ultrasonic sensors need to be placed on a fitting that is in the center of the tank.
What are the installation constraints?
All telemetry solutions on tanks need to have access to a fitting. If it is available and that there are no network issues, the sensor installation can be done in 30mn.
In the absence of a fitting, and as long as safety regulations will allow it, there is the possibility to drill a hole on the top of the man hole, create a fitting, and insert a pressure sensor at the bottom of the tank. In case there is already a device using the only available fitting, the technician can install a “T” to allow a pressure sensor to be inserted.
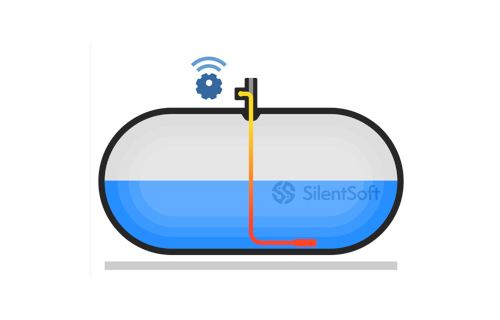
Ultrasonic sensors need to be placed on a fitting that is in the center of the tank.
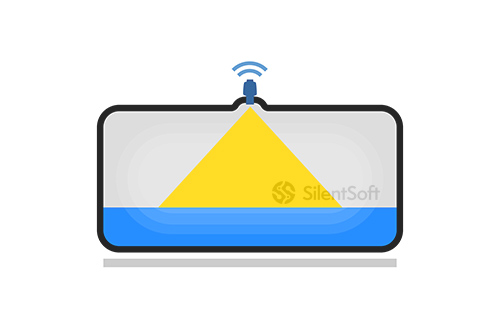
If it is too close to the edge (as shown below), or if the tank has a rectangular shape with internal metallic reinforcements, there is the possibility that the radar interprets that the tank is still full when in fact it is empty.
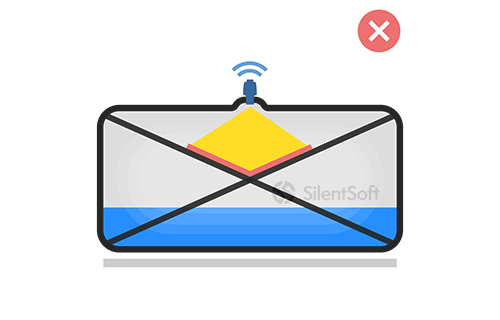
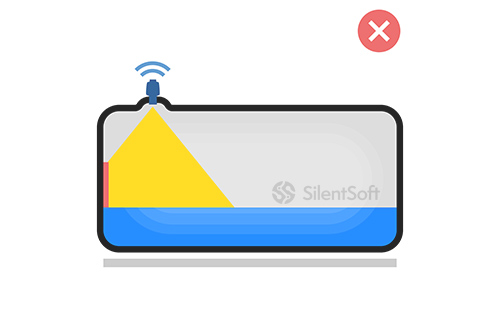
Should these cases occur, there is the possibility to drive the radar signal through a PVC tube to avoid interferences. The solution works when there are no physical constraints inserting the PVC tube to the bottom of the tank. Some tanks in cellars or basements do not have sufficient height between the top of the tank and cellar / basement ceiling for installation of such a solution The installer will have to drill small holes (too large holes could have an impact on the ultrasonic readings) at the top of the PVC tube to allow the air to escape when there is a filling.
Current solutions used for ultrasonic sensors require a fitting of at least 2 inches. Anything smaller will need a pressure sensor solution that can adapt to a one inch fitting. PVC tubes also need to be placed away from the filling point. The force of the pressure can damage or misplace the PVC tube.
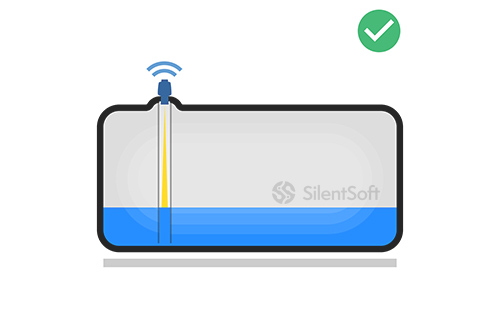
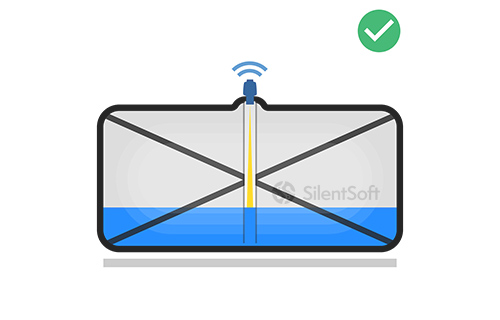
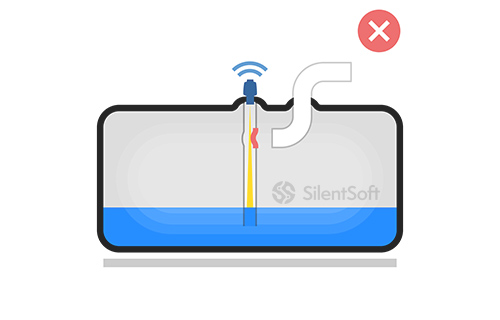
Installation optimizations
SilentSoft has introduced solutions that allow to manage 2 tanks with one transmitting device. This will reduce the cost of the telemetry solution when two tanks are physically side by side.
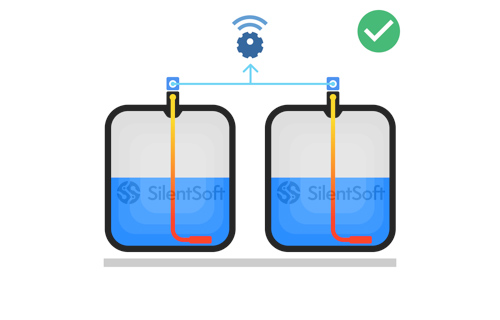
How to manage an installation on site?
The ideal situation before performing any installation is to have a picture of the tank situation / location and a picture of the man hole to check if there are fittings available. In all cases the installer needs to have fitting adapters pending the tank configuration, “T” adapters, in case the fitting is already used. Placing a PVC tubes on ultrasonic sensors have transport and installation constraints.
SilentSoft installers will always seek to install the most cost effective solution by default. On top of adapting the sensor solution to the tank configuration, the technician has to select the best available network. There is the choice of Public Cellular Wide Area Networks (2G/3G/4G) vs. Low Power ones (LoRa, Sigfox, NB-IoT for example). Some transmitting devices give the option to add an external antenna. Pending the product measured there may be the need to have ATEX certified sensors and modems. This will also drive the choice of the device prior installation.